Last Updated APRIL 2024
Mastering the Art of Waste Walks: From Preparations to Direct Observations
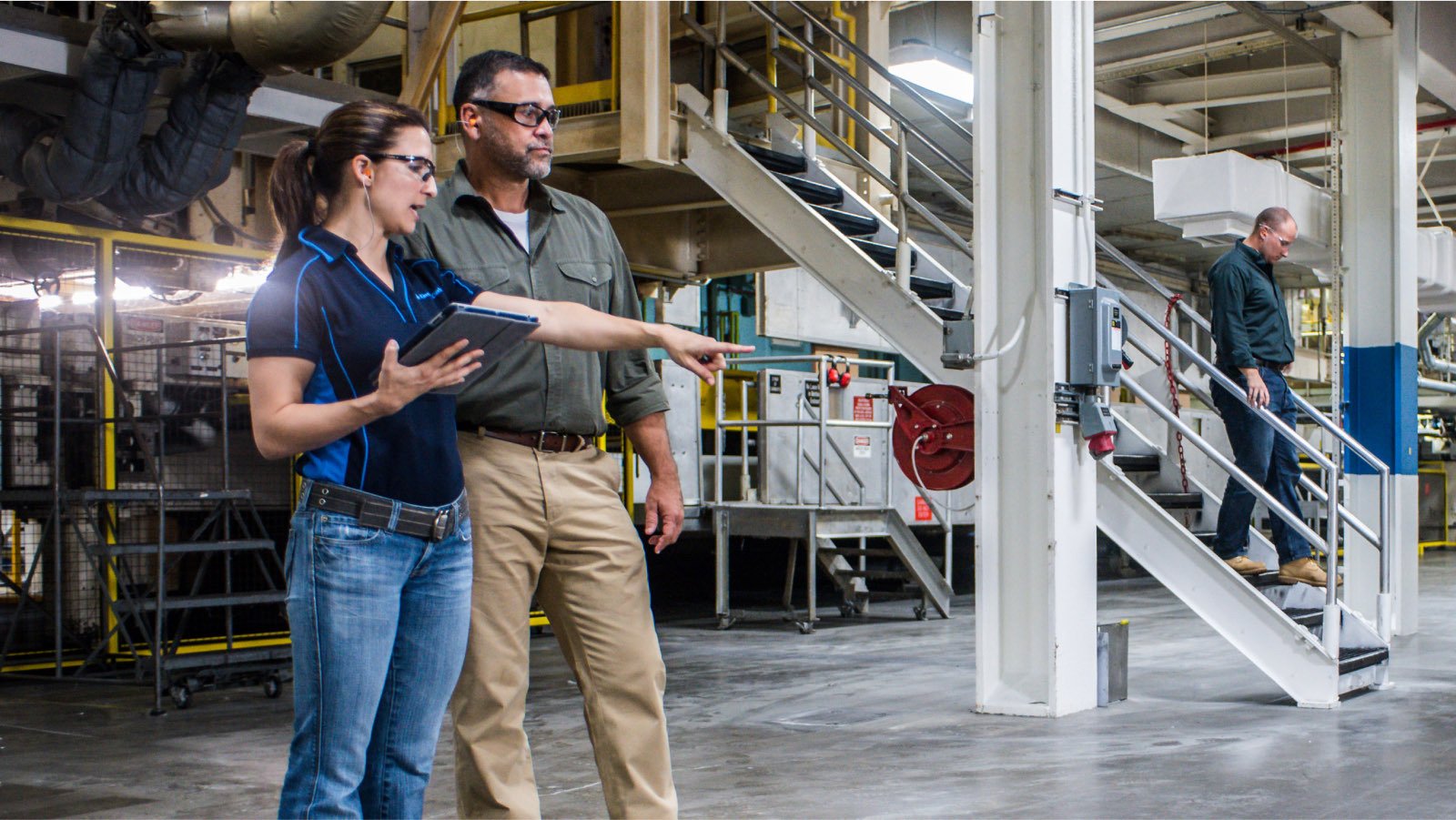
To kickstart your waste reduction journey, discover how implementing regularly scheduled waste walks uncovers hidden inefficiencies and waste streams in your operations — ultimately, improving performance company-wide.
In this post, we'll cover:
- » 8 Wastes in a Lean Environment
- » Waste Walk Preparation Tips
- » Navigating the Waste Walk
- » Waste Walk Do's & Don'ts
Sustainability has become a call to arms for CEOs and organizations worldwide. The enthusiasm is tangible as organizations declare a commitment to environmental stewardship. They set ambitious sustainability goals, launch new initiatives, and invest substantial resources. Yet, despite these efforts, momentum wanes, leading to a frustratingly common setback.
Research by Bain & Company reveals that only 2% of organizations have met or exceeded their sustainability program's objectives.1 It's not due to a lack of effort, but the journey to sustainability is proving far more challenging than anticipated.
Enter the waste walk — a strategic exercise that uncovers hidden inefficiencies and waste streams within an organization's operations.
While striving for these “big picture” goals, we often underestimate the significant impact of optimizing current processes.
Enter the waste walk — a strategic exercise that uncovers hidden inefficiencies and waste streams within an organization's operations . It's rooted in the concept that before you can solve a problem, you must first see and experience it firsthand.
By embracing waste walks and welcoming leadership into the operational fold, organizations can uncover transformative possibilities to streamline processes, enhance productivity, and develop actionable short-term and long-term waste reduction plans.
Let's delve into the process of preparing for and executing a successful waste walk to aid you in your waste reduction journey.
Decoding your Waste — the Eight Wastes in a Lean Environment
A core aspect of waste walks involves understanding the lean concept of waste. Waste is anything that doesn't contribute value to your business, operations, customer satisfaction, or growth — such as wasted time, effort, space, or resources.
Watch for these eight wastes during your waste walk as they represent tangible barriers that impact efficiency and productivity. While not all may be present in every scenario, being mindful of these sets the stage for more effective and streamlined operations.
Here are the eight wastes to watch for:
Transportation
Unnecessary movement of goods or materials, such as shifting products between locations or excessive tool movements.
Inventory
Excess stock beyond immediate requirements, tying up capital and space.
Motion
Unnecessary human movements, like excessive walking for supplies or awkward movements at workstations.
Waiting
Idle people, information, or equipment due to process delays, impacting productivity.
Overprocessing
Idle people, information, or equipment due to process delays, impacting productivity.
Overproduction
Going beyond necessary or providing additional value not required by customers.
Defects
Faulty products or services that don't meet customer requirements, resulting in rework and added expenses.
Skills
Underutilized employee skills and knowledge due to poor job allocation or insufficient training.
Before beginning the waste walk, ensure your team understands these eight wastes to guarantee more focused and meaningful insights.
Setting the Stage — Waste Walk Preparation Tips
A successful waste walk begins with thorough preparation. Here's how to get your team ready for effective exploration:
Define Clear Objectives:
Before starting the waste walk, outline specific objectives. These objectives act like a compass, guiding the walk toward precise goals that align with broader organizational improvements.
Build the Right Team:
Create a diverse team with leaders, supervisors, cross-functional reps, and executives for a more complete view. Define each person's roles and restrict each task to a maximum of two people to prevent disruptions.
Foster Open Communication and Ownership:
Create a communication channel where team members can share insights, ideas, and concerns. Encourage everyone to take ownership of their observations and proposed solutions for greater engagement and collaborative problem-solving.
Conduct a Pre-Walk Meeting:
Before the walk, bring the team together to reaffirm goals and duties. Practice waste walk procedures, especially for those new to it, and refer to the current process map if available.
A process map visually displays a process's steps, interactions, and dependencies. Include crucial details — inputs, outputs, decision points, and department handoffs — to capture the process and spot potential waste points.
Equip Your Team:
Equip your team with essential tools like paper, tablets, or cameras for visual documentation. Use a standardized observation sheet for uniformity throughout the waste walk.
Preparation sets the stage for a successful waste walk. Clear objectives, an engaged team, and the right tools empower your team to conduct purposeful observations to uncover inefficiencies and drive meaningful improvements.
Navigating the Waste Walk — Principles for Success
Remember two guiding principles for a successful waste walk: observe closely and question why. Stay curious, ask open-ended questions, and foster collaboration throughout.
When entering the work area or "Gemba," communicate your intent to observe workflows without causing disruptions. If Lean practices are new, reassure employees that the focus is on improving processes, not individual performance.
Engage directly with staff involved in the process, encouraging them to share insights and ideas through questions like:
- Why do we approach tasks this way?
- How can tasks be more efficient?
- What challenges do you face in your work?
- If given a chance, what changes would you make and why?
Allocate ample time, around 30-45 minutes, to observe work being done without interruptions. Take detailed notes during the observation, noting bottlenecks, delays, or inefficiencies. Visual cues like excessive movement or disorganized workspaces often reveal potential waste areas.
Afterward, discuss your findings as a waste walk team. Compare observed waste with the current process map, identify system-level issues, and prioritize the most impactful solutions.
The real value of a waste walk lies not just in observation but in turning these insights into actional plans for short-term and long-term improvements.
Waste Walk Do's and Don'ts
Waste Walk Do's | Waste Walk Don'ts |
---|---|
Do schedule regular waste walks to establish a routine. | Don't problem-solve during the observation phase. |
Do seek clarification if something observed isn't clear. | Don't let distractions like phones or emails divert your focus during the walk. |
Do communicate openly throughout: before, during, and after. | Don't neglect to follow through on observations with action plans. |
Do visit all areas as every job function is important to the process. | Don't schedule waste walks during critical or busy times. |
Do document what's happening vs. what should be happening. | Don't solely rely on interviews; actively observe tasks being performed. |
Do gather the waste walk team after to share findings. | Don't perceive this as evaluating performance; but rather the process. |
Embrace the Power of Transformative Insights
Continuing your waste reduction journey requires ongoing monitoring, refinement, and a culture that values continuous improvement. Waste walks drive positive change by engaging employees at all levels and fostering cross-functional collaboration, recognizing the importance of insights from the bottom up.
With this knowledge, your team can use data-driven insights to identify and remove the root causes of waste, significantly impacting organizational performance. Embrace waste walks to guide your organization toward efficiency, sustainability, and an ever-evolving approach to improvement.
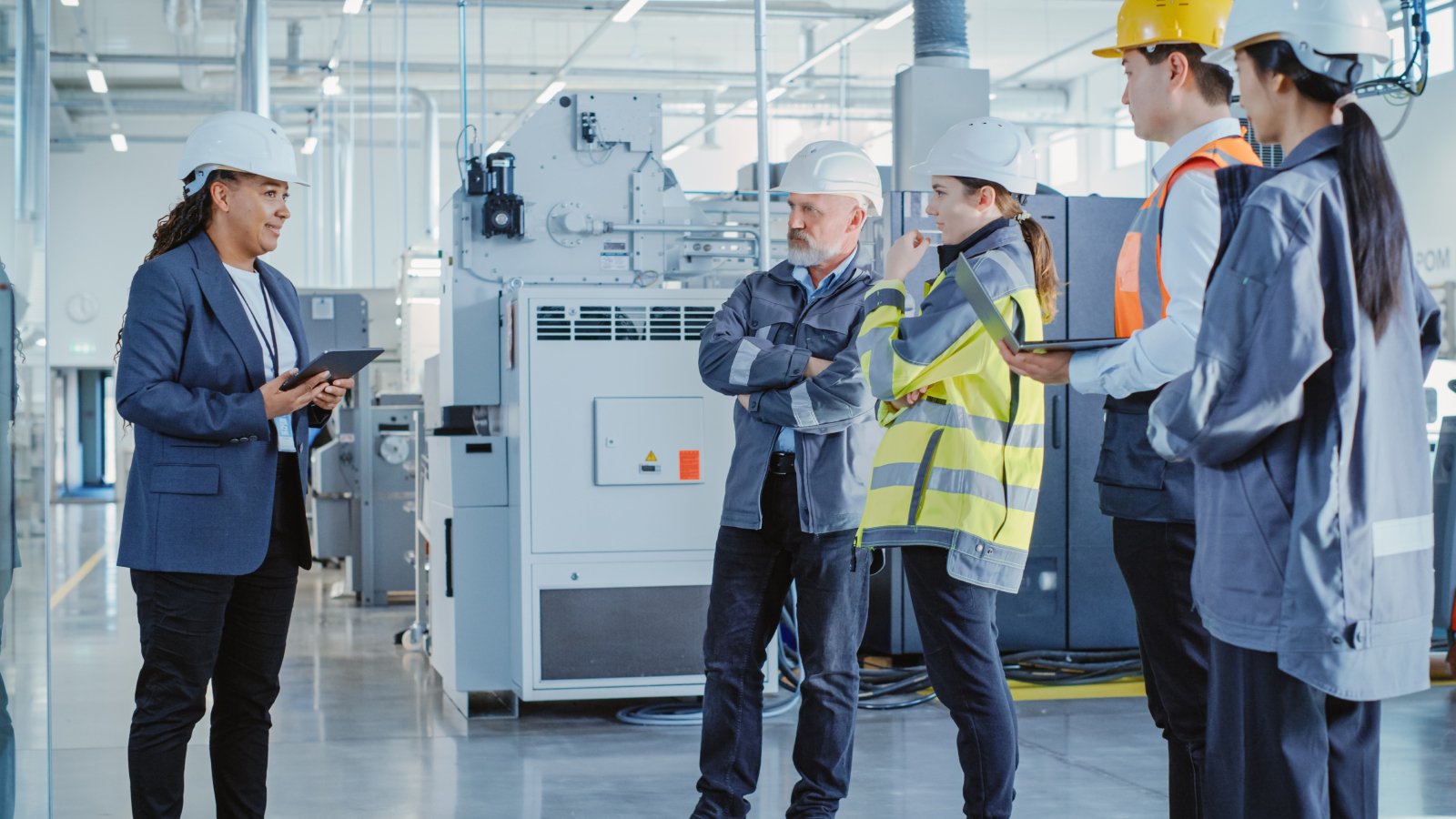
Beyond the Walk
You've completed your waste walk, so what happens next? Learn how to maximize the impact of your insights to turn them into action plans that further your sustainability goals.