Last Updated JULY 2023
Reusable Cleanroom Apparel and the Contamination Risks
Based on a recent study, the Bacterial Filtration Efficiency (BFE) of reusable cleanroom apparel degrades significantly after the garment has gone through wash and irradiation cycles. This poses a real yet invisible contamination risk to aseptic manufacturing environments.
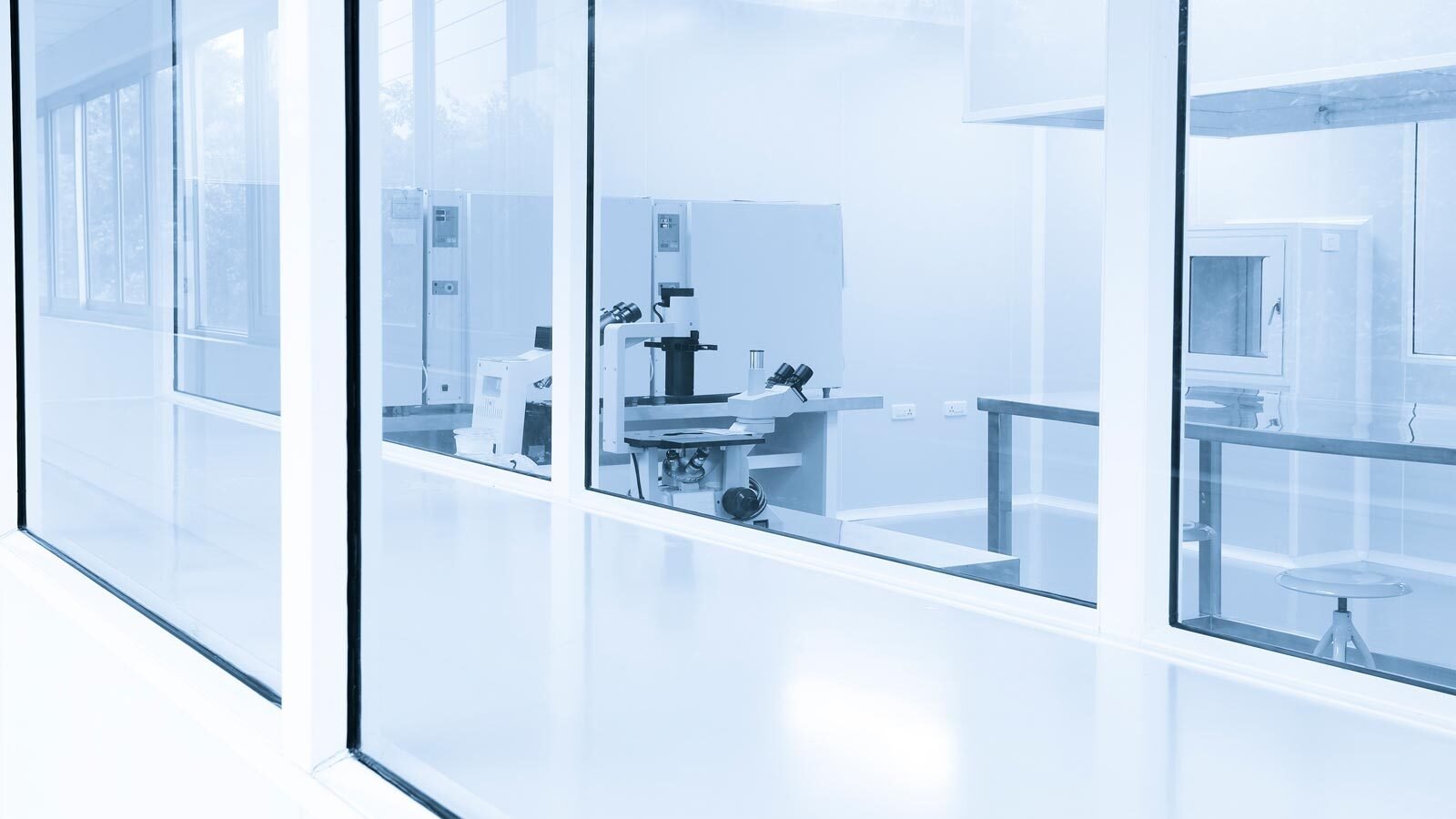
The Contamination Risks Posed by Reusable Cleanroom Apparel
A significant cost to pharmaceutical manufacturing is process contamination. Nothing is more serious than a contamination event in a cleanroom. Contamination can lead to expensive shutdowns and increased production expenditures, as well as recalls and potential loss of life.
People are the largest contributor to particle contamination in any cleanroom, accounting for 46 percent of all particle contamination. Humans shed and spread millions of particles throughout the day. Body regenerative processes, such as skin flakes, oils, perspiration and hair, all can contribute to cleanroom contamination.
Wherever there are people, there is a risk of microbial contamination.
This risk can be mitigated by using sterile cleanroom apparel that protects the environment from viable particles such as bacteria and yeast, and nonviable particles such as hair, dead skin cells, and dandruff. For this reason, it’s essential that cleanroom operators select apparel that provides the highest levels of contamination control.
Choosing the right type of apparel is paramount. But what if the garment itself poses a hazard to the cleanroom environment? Testing by Kimberly-Clark Professional™ found that the barrier on reusable protective apparel declined after multiple washing, drying and sterilization cycles. This barrier decline poses a significant contamination risk for cleanrooms.
Cleanroom Apparel
Cleanroom apparel falls into two main categories: single-use disposable apparel and reusable laundered apparel.
Single-Use Apparel
Single-use apparel is made from two types of fabric: 1) flash-spun polyethylene fabric, which provides filtration efficiency for sub-micron sized particles and microorganisms and is suitable for light splash protection from non-hazardous liquids, and 2) spunbond melt blown spunbond (SMS) fabric, which has outer layers of spunbond polypropylene for strength and cloth-like comfort, and middle layers composed of a matrix of microfibers, which creates a strong barrier for particles and liquids.
Reusable Apparel
Reusable cleanroom apparel is typically made from woven polyester-blend fabrics, which may degrade after multiple laundering and sterilization cycles. Testing conducted by Kimberly-Clark Professional™ used garments that were randomly selected from pharmaceutical customers. The testing results showed a decline of more than 25 percent in Bacterial Filtration Efficiency (BFE) after an average of five washings. This presents a real yet invisible contamination risk to aseptic manufacturing environments.1
The testing also found:- 100 percent of the worn sterile reusable garments tested showed a decline in BFE after washing.
- The filtration efficiency of the reusable garments was typically less than 70 percent.
- Fabric degradation was visible at the sub-micron level – enough to allow bacteria to penetrate the material. The product declined more rapidly than expected and that decline continued through multiple wash cycles.
- The total cost of ownership for reusable cleanroom apparel was much higher than projected.
- The average number of wash cycles was much lower than expected.
Results Confirmed by Additional Testing
Kimberly-Clark Professional™ conducted comparative testing of disposable and reusable cleanroom apparel. The testing method involved covering a container with a swatch of reusable apparel material and another with a swatch from a Kimberly-Clark Professional™ disposable apparel fabric.2 The containers were then sprayed with an aerosolized form of Staphylococcus aureus bacteria. After 24 hours, the material was removed and the number of colony-forming units of bacteria were counted to measure the number of bacteria that penetrated through to the test medium. The results:
- The disposable fabric maintained its 95 percent BFE.
- The reusable fabric had a 68 percent BFE.
Additional Concerns
The laundering process for reusable cleanroom apparel involves multiple processing steps – such as sorting, multiple wash cycles, drying, cool-down and inspection – which all put the fabric under additional stress. This is repeated each time the gown is serviced. Therefore, the laundering process itself creates channels for bacteria to pass through. Test data for the BFE of reusable apparel is typically based on new apparel, not on apparel that has been washed and sterilized multiple times. The filtration efficiency and the lifespan of the apparel do not appear to be consistent with what is being observed in use.
Single-Use Apparel Benefits
Disposable apparel offers a few other advantages over reusable apparel, including:
- Predictability – These garments are washed once to guarantee optimal, predictable performance for each garment.
- Data transparency – Data on disposable garments is available.
- Ease of donning – Unlike reusables, some disposable apparel is designed with innovative features that keep the garment from touching the floor during the donning process.
- Comfort – The Kimberly-Clark Professional™ SMS fabric is cool and breathable.
- Easy recycling – The RightCycle Program enables cleanrooms to recycle single-use garments and is the first large-scale recycling effort for non-traditional cleanroom waste. It mitigates waste and assures cleanrooms of a sustainable apparel solution. The RightCycle Program turns previously hard-to-recycle nitrile gloves and single-use apparel items from Kimberly-Clark Professional™ into durable consumer goods.
- Consistent Performance – Single-use apparel provides performance and consistency to ensure that the highest levels of sterility are being met.
- Vacuum-sealed – This method ensures sterility.
Conclusion
The test findings detailed here cast doubt on the efficacy and reliability of reusable protective apparel and its ability to meet cleanroom standards after laundering. All sterile reusable apparel tested showed a decline in Bacterial Filtration Efficiency (BFE) after washing. By contrast, single-use disposable apparel is washed once, guaranteeing optimal, predictable performance for each garment.
When selecting apparel for an aseptic manufacturing environment, it’s essential to choose cleanroom apparel that offers the highest level of BFE. Purchasers would be wise to consider these study results and choose sterile, disposable apparel for their facilities.
1 ASTM F2101-14 Standard Test Method for Evaluating the Bacterial Filtration Efficiency (BFE) of Medical Face Mask Materials, Using a Biological Aerosol of Staphylococcus aureus
2 Kimtech* A5 fabric